Как сделать деталь, напечатанную на 3D-принтере, более прочной
Как нам всем хорошо известно, детали, напечатанные на обычном домашнем 3D-принтере, получаются не такими прочными и служат не так долго, как оригинальные. Мы подумали, что было бы здорово научиться как-нибудь укреплять напечатанные детали, и немного над этой идеей поработали.
Такие более прочные детали позволят нам использовать их в реальном деле, при высокой нагрузке. Тогда, вместо того чтобы искать оригинальные детали на замену сломавшимся в гаджетах, роботах, машинах, механических игрушках или для любого разрабатываемого проекта, мы сможем просто напечатать их.
Необходимость в разработке такого руководства возникла у автора тогда, когда он купил на eBay велосипедные подвесные сумки. Одну для подруги, другую для себя. Крепление сумок подразумевало, что руль имеет толщину в один дюйм (2,54 см), и едва подходило к женскому велику. Руль же мужского велосипеда имел диаметр 3,15 мм, и на него крепление не налезало.
Поэтому появилась мысль изготовить деталь по размеру соответствующего крепления, напечатав ее на 3D-принтере.
Шаг 1. Требующаяся деталь
Вот узел, который нужно воспроизвести на 3D-принтере.
Чтобы что-то напечатать, для начала требуются файлы 3D-модели. Их, соответственно, нужно найти и скачать в интернете или же разработать самостоятельно. Второй вариант представлялся единственно возможным, поскольку готовых 3D-моделей для такой специфической детали найти невозможно, и нужно было модифицировать ту, которая имелась, так, чтобы она налезала на руль.
Однако всем прекрасно известно, что напечатанные на 3D-принтере детали прочностью не отличаются. Напечатанный обычным способом данный узел получился бы не настолько прочным, чтобы надежно держать тяжелую сумку на тряской дороге. Тогда возникла мысль как-то укрепить эту деталь, придав ей достаточно прочности.
Автор несколько лет занимался судомоделированием и имел возможность убедиться, насколько слои стекловолокна и эпоксидки делают более крепкими даже тонкие фанерные детали, в результате чего они без проблем выдерживают высокие нагрузки.
Поэтому и в данной работе было решено задействовать стекловолокно и эпоксидный клей-смолу.
Первоначально планировалось снять чертеж детали, внести необходимые изменения по размерам и покрыть все стекловолоконной тканью с эпоксидным клеем. Итак, приступим к моделированию.
Шаг 2. Проект первый
Деталь должна быть такой. Все размеры подогнаны, всё в целом увеличено и утолщено. Увеличены и поверхности, чтобы на них можно было наклеить стекловолокно.
Кроме того, на каждой из сторон предусмотрены желобки, чтобы заполнить их эпоксидкой для придания еще большей прочности. Смоделированы также сквозные отверстия, чтобы части узла было проще соединять друг с другом и чтобы стекловолокно и смола соединяли их изнутри.
Деталь напечатана на принтере Up и проверена на предмет того, подходит ли она по размерам.
Тип заполнения выбран решетчатый, что позволило оставить достаточно пустого пространства внутри детали. В обычной ситуации это уменьшает прочность, но сделано это было сознательно. В детали просверлено еще несколько отверстий, чтобы позволить эпоксидному клею проникнуть внутрь и укрепить ее.
Шаг 3. Нанесение стекловолокна и эпоксидного клея на первый проект
Это самая грязная часть работы. С эпоксидкой и стекловолокном работать сложно. Всё везде липнет так, что потом почти не отмоешь.
Сначала полоски стекловолоконной ткани были наклеены на обе половинки детали, чтобы они лучше скреплялись.
Затем всё было выложено на кусок нейлона, поскольку эпоксидная смола, к счастью, к нейлону прилипает не так смертельно. После этого эпоксидка была нанесена на поверхность детали, вырезан соответствующей формы и размера кусок стекловолоконной ткани, поверх которой был опять-таки нанесен эпоксидный клей. Клея было столько, что стекловолокно стало прозрачным.
Вся эта процедура повторилась для другой стороны детали, после чего смола день застывала. Даже немного больше, чтобы всё скрепилось намертво.
Шаг 4. Еще эпоксидки для дополнительного укрепления с боков
Решено было также добавить еще эпоксидного клея в специально предусмотренные для этого торцевые бороздки.
Шаг 5. Проект второй
При разработке первого проекта имелось в виду, что деталь через просверленные в ней дополнительные отверстия будет частично заполнена эпоксидной смолой, а снаружи ее будет держать пропитанное эпоксидкой стекловолокно. В процессе печати первой детали родилась идея смоделировать только ее оболочку, а внутри все вообще сделать только из эпоксидного клея и стекловолокна.
И вот, пока первый проект застывал, решено было приступить к моделированию второго. Хотелось сравнить оба варианта в плане прочности и легкости в изготовлении. Во втором проекте в заполнении двух фрагментов детали (для крепления нужно две части) был использован различный подход.
На фото видно, что второй проект – это пустая оболочка со стенками в 1 мм толщиной. Округлый фрагмент отделен от большего, чтобы упростить процесс заполнения. Его нужно потом, когда эпоксидка будет застывать, закрепить винтами.
Шаг 6. Заполнение второго проекта эпоксидкой и оптоволокном
Для начала было мелкими кусочками нарезано стекловолокно, и получившимися клочьями обе части детали заполнены чуть больше, чем наполовину. Затем нужно по каплям добавлять эпоксидный клей и немного придавливать обрезки, чтобы они хорошо пропитывались.
Шаг 7. Заполняем дальше проект 2. Фрагмент 1
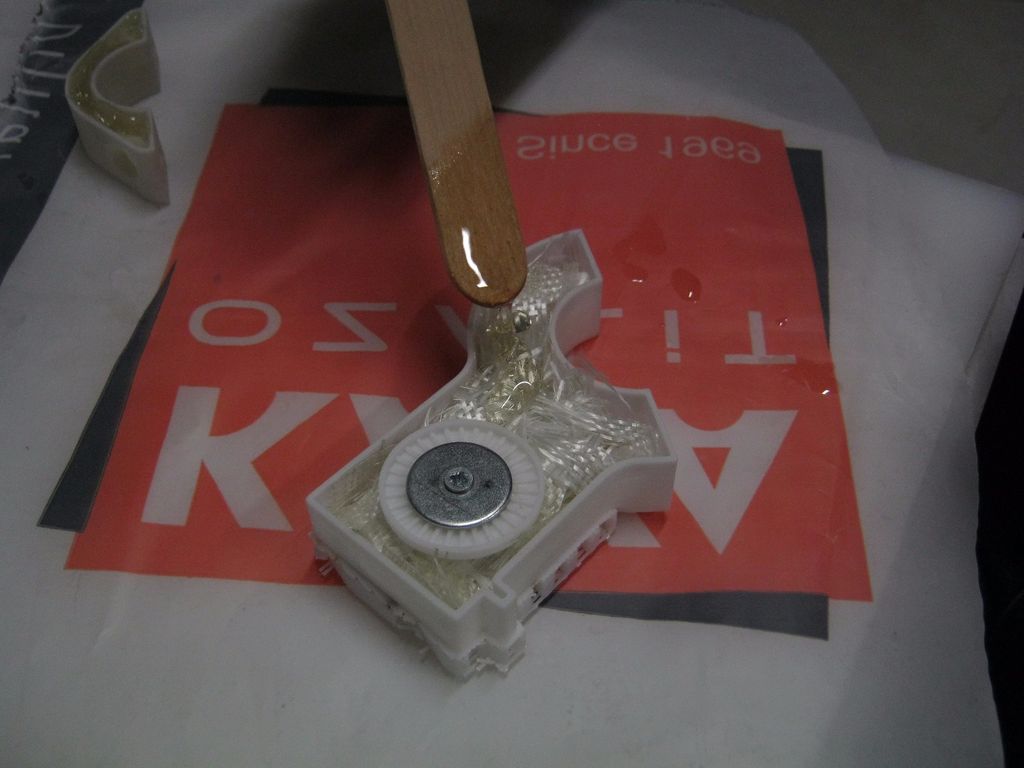
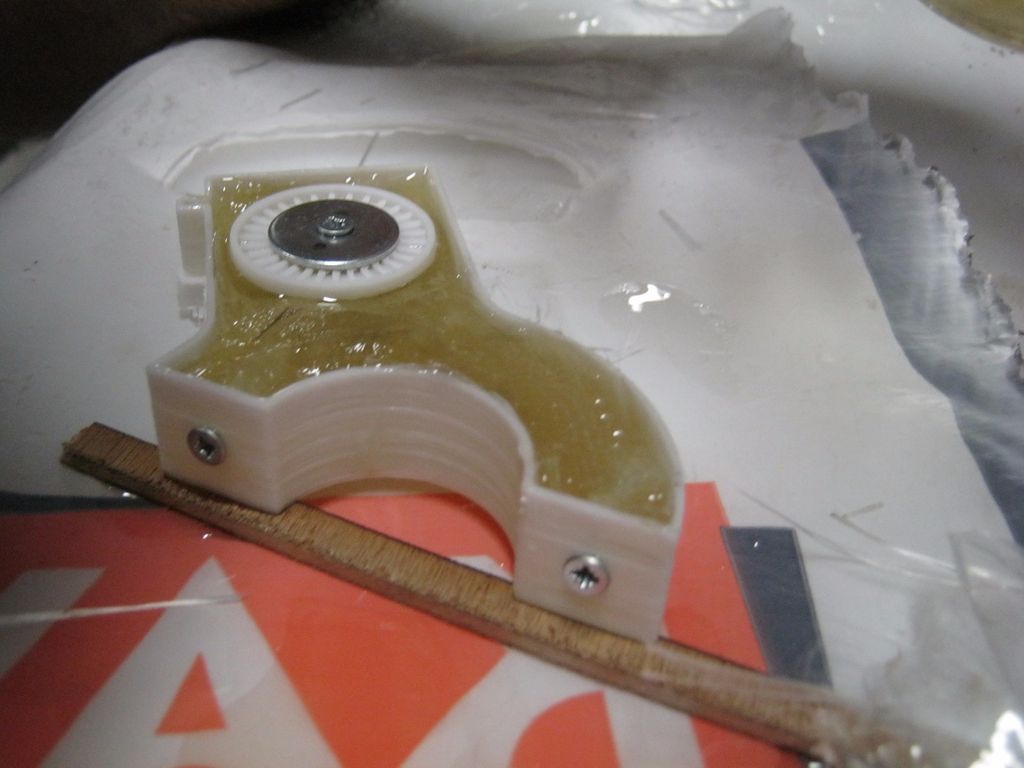
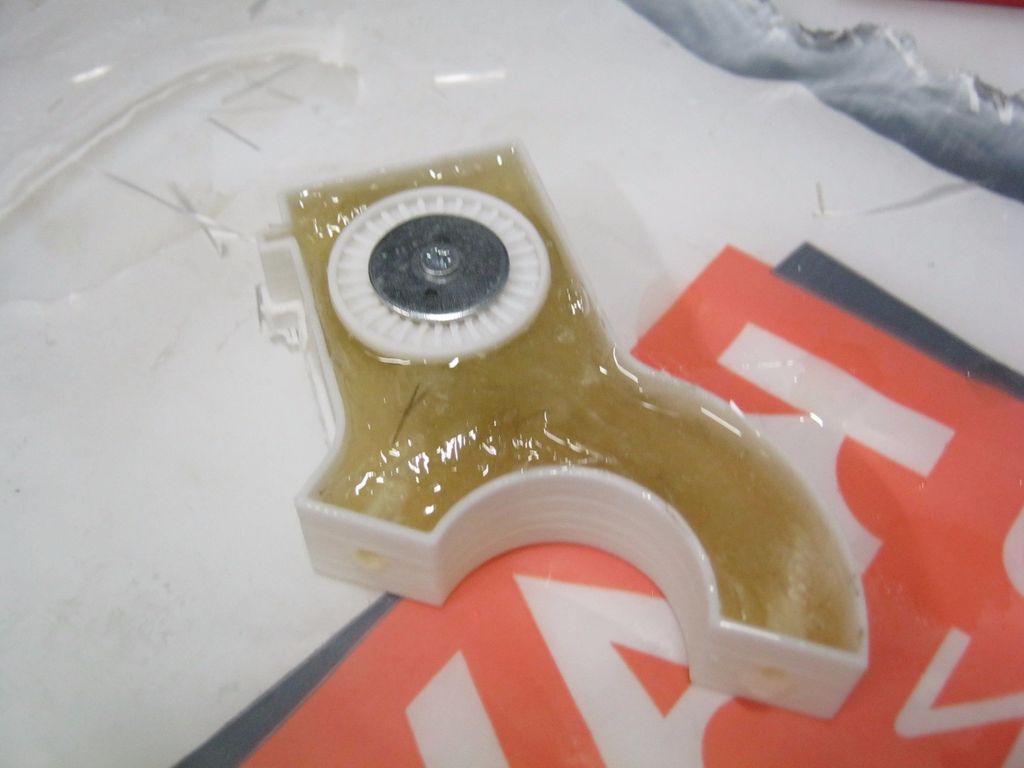
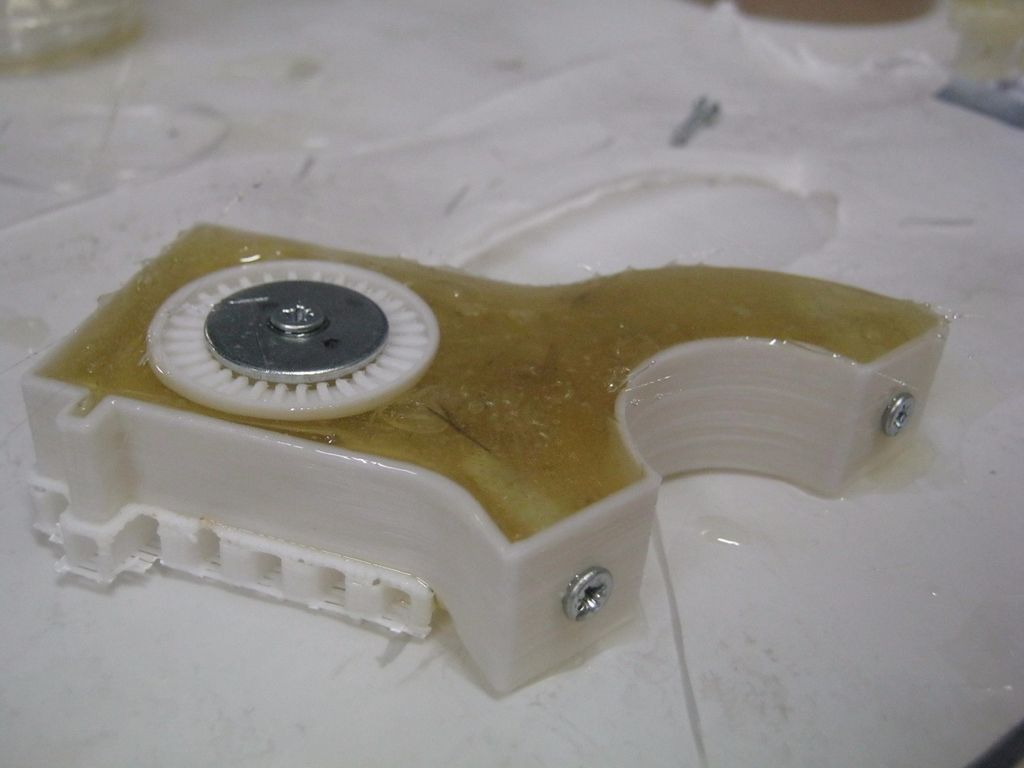
Продолжаем капать и утаптывать, пока вся стеклоткань не пропитается, после чего добавляем еще обрезков стеклоткани, повторяя этот шаг до окончательного заполнения детали. Теперь закрепим винтами второй фрагмент детали. В конце концов уровень смеси эпоксидки и стекловолокна должен быть до краев.
Почти то же самое для меньшего, округлого фрагмента.
Шаг 8. Заполняем проект 2. Фрагмент 2
Для этого фрагмента применен несколько другой подход: деталь не заполнялась с самого начала наполовину. На дно был уложен только один слой стеклоткани, затем еще один – с перехлестом на края. Эти слои пропитывались эпоксидкой до тех пор, пока не стали полностью прозрачными, после чего на них один за другим укладывались и придавливались, чтобы впитали клей, следующие слои. Немного эпоксидки добавлялось через каждые 2-3 слоя.
Первый способ давал нам деталь, внутри которой больше эпоксидной смолы и чуть меньше стекловолоконной ткани. При втором способе в детали больше стекловолокна и меньше эпоксидки между слоями.
Шаг 9. Теперь всё должно застыть
Периодически детали проверялись, в образующиеся при впитывания смолы пустоты добавлялось еще смолы. Где надо, добавлялось стекловолокна. На полное застывание ушел примерно день. В продаже есть эпоксидные клеи, которые застывают быстрее, можно также добавить больше отвердителя, чтобы ускорить процесс. Мы, однако, этого не рекомендуем, потому что это только осложнит работу и будет мешать клею проникнуть во все углы.
Шаг 10. Сборка готового узла
Детали получились довольно неплохими, особенно по второму проекту. Крепление их на сумку прошло без проблем. Подошли отлично. Теперь нужно закрепить сумку на велосипед.
Шаг 11. Удаляем пластиковые части
Этот шаг на самом деле не предусматривался. Предполагалось просто использовать напечатанные на 3D-принтере и укрепленные детали. Но когда дело дошло до ошкуривания, напечатанная «кожица» просто стала отламываться по углам, остальное тоже снималось без проблем. «Кожица» эта никакой дополнительной прочности не давала, поэтому и была практически полностью снята, и деталь стала композитной эпоксидно-стекловолоконной.
Шаг 12. Итоги
Деталь без проблем продержалась во время 20-дневной поездки по Швеции, Польше, Германии и Дании. Передняя сумка было все время до отказа заполнена едой, было пройдено немало ухабистых дорог. Детали прослужили на отлично и по-прежнему крепче камня.
Вот еще несколько полезных замечаний.
- Интересно, что эпоксидка не очень хорошо прилипает к ABS. Именно поэтому дополнительные отверстия, через которые она будет проникать внутрь и скреплять конструкцию, просто обязательны.
- Укреплять деталь снаружи гораздо сложнее, чем заполнять ее. Времени на первый вариант уходит масса, но заполненная деталь получается легче. Бесспорно, укрепленная деталь значительно прочнее, чем просто напечатанная и не укрепленная. Это легко проверить, если испытать на скручивание укрепленную и не укрепленную детали. Укрепленная подобна камню, обычная легко меняет форму.
- Второй метод укрепления гораздо проще и дает гораздо более опрятный результат. После застывания смолы почти ничего не надо чистить. А то, что получилось, имеет крепость гранита!
- Оба варианта заполнения при различных количествах стекловолокна дают одинаковое ощущение прочности и массивности. Однако тот, где волокна больше, теоретически и почти без сомнений должен выдерживать больший вес.
- По второму проекту узел получается более тяжелым, поскольку внутри он полностью состоит из стекловолокна и эпоксидной смолы. Вес немного уменьшается после удаления окружающего пластика. При этом, впрочем, изменятся и размеры детали. Поэтому о размерах нужно подумать заблаговременно и учесть снятие пластика при моделировании.
- Во втором проекте тоже можно предусмотреть желобки-бороздки и пустоты, тогда вес удастся снизить.
Перевод статьи Strengthening a 3D Printed Part с сайта Instructables.com